Table of Contents
TL;DR
Information | |
---|---|
Project Brief | LURA, the Leeds University Rocket Association, used RapidDirect’s 5-axis CNC machining and turn-mill compounding techniques to create intricate engine parts essential for their victory in the National Race to Space Propulsion Competition. |
Industry | Aerospace |
Technology | CNC machining |
Materials | Stainless steel, Aluminum |
Surface Finishing | As Machined |
Challenges | 1. Tight Deadline: The two-week span posed a challenge for delivering intricate parts. 2. Intricate Design: Rocket engine parts, especially combustion chambers, were deemed “manufacturable”. Besides, there are many oblique holes and grooves. 3. Tight Tolerance: The project required a challenging precision of +/-0.07 mm. 4. Material Issues: Unique thermal needs dictated using unconventional materials, especially in the combustion chamber. |
Solutions | RapidDirect employs 5-axis CNC machining and turn-mill compounding techniques to accurately machine complex geometries, such as oblique holes and grooves. |
The Result | The engine parts delivered within 7 days exceeded LURA’s expectations. |
“As for the machined parts, we are exceedingly pleased with the precision and quality of the work delivered. Without exception, all parts seamlessly fit together as intended, and the surface finishes surpassed our specified requirements, reflecting a level of craftsmanship that exceeded our expectations.”
– Dom Buta
Introduction
The new space age marks a confluence of daring dreams, unmatched innovation, and seamless collaboration. This is epitomized by the stellar partnership between LURA ( Leeds University Rocket Association) and RapidDirect. The ambitious goal set by LURA to make a mark in the world of aerospace competitions met its match in RapidDirect’s commitment to precision, timely delivery, and relentless innovation. This case study highlights the journey of two pioneering entities joining hands to challenge the boundaries of possibility.
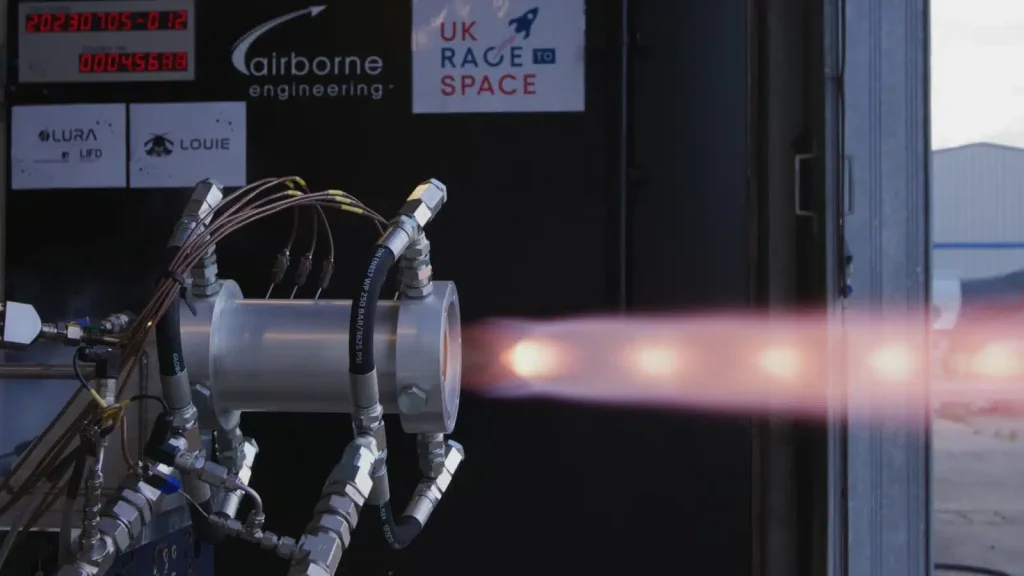
LURA’s Silverback Programme
Founded in March 2021, LURA aimed to equip the next generation for Mars exploration and extend aerospace understanding to all students. Their immediate goal was to shine at the esteemed “Spaceport America Cup” A cornerstone of this mission was the Silverback Project, resulting in their debut engine, “LOUIE.” Prepared for the Race to Space National Propulsion Competition and produced by RapidDirect, “LOUIE” symbolized LURA’s deep aspirations in rocket design.
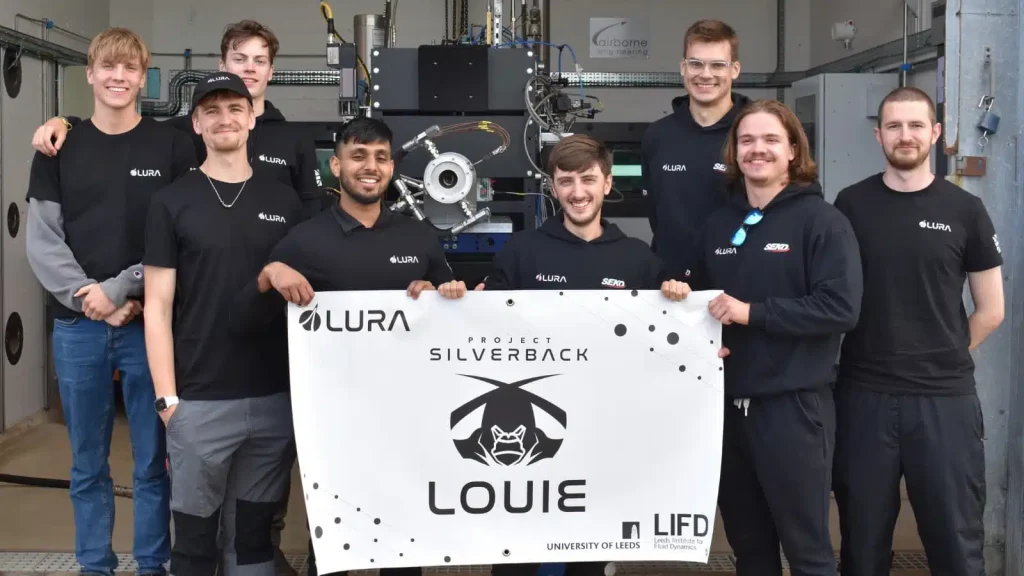
Challenges Encountered
LURA’s engine project was no ordinary endeavor. The production of such intricate components, each requiring specialized turning and milling operations, posed a significant challenge. Time was of the essence, and almost all potential machining centers were either hesitant or proposed considerable modifications to the project’s set parameters. Moreover, the project demanded not only high accuracy and challenging geometric tolerances but also the manufacturing of a combustion chamber, which many experts believed was unfeasible.
Budgetary considerations added another layer to the challenge. While some global quotes were aligned with LURA’s specifications, the costs proved prohibitive. RapidDirect emerged as the beacon in this scenario, promising precision, meeting budgetary constraints, and agreeing to a tight timeline.
- A diverse range of complex features
- Stringent geometric tolerances
- A demanding delivery timeline
- The utilization of non-standard materials for certain parts
“RapidDirect not only committed to manufacturing all of our parts with only minor adjustments but also offered competitive costs that fit within our budget, all while ensuring strict adherence to our tight timelines. “
RapidDirect’s Innovative Solutions
Recognizing the weight of LURA’s aspirations and the technical intricacies of the ‘LOUIE’ engine, RapidDirect approached the challenge with a mix of innovation, pragmatism, and unwavering commitment.
Dedicated Team for Silverback Project
To ensure the highest level of focus and expertise, RapidDirect set up a dedicated team specifically for the Silverback Project. Comprising of seasoned engineers and CNC specialists, this team was responsible for every minute detail of the manufacturing process.
Re-Evaluation of Tolerances
The team diligently analyzed LURA’s design specifications, especially the stringent tolerances. The original tolerances posed a risk of scrapping during machining, so RapidDirect proposed slight modifications. These weren’t radical changes but calculated adjustments ensuring the components would be perfectly fit for purpose, while still adhering to machining values.
Innovative Machining Techniques
To cater to the complexity of the engine parts, the team employed a turn-mill combination technique. This first sculpted the primary shape of the components. But the magic was in the details. Special fixtures were made exclusively for the Silverback Project. Subsequently, using 5-axis machining, the team meticulously carved out the grooves or drilled oblique holes, ensuring the strictest of tolerances were maintained.
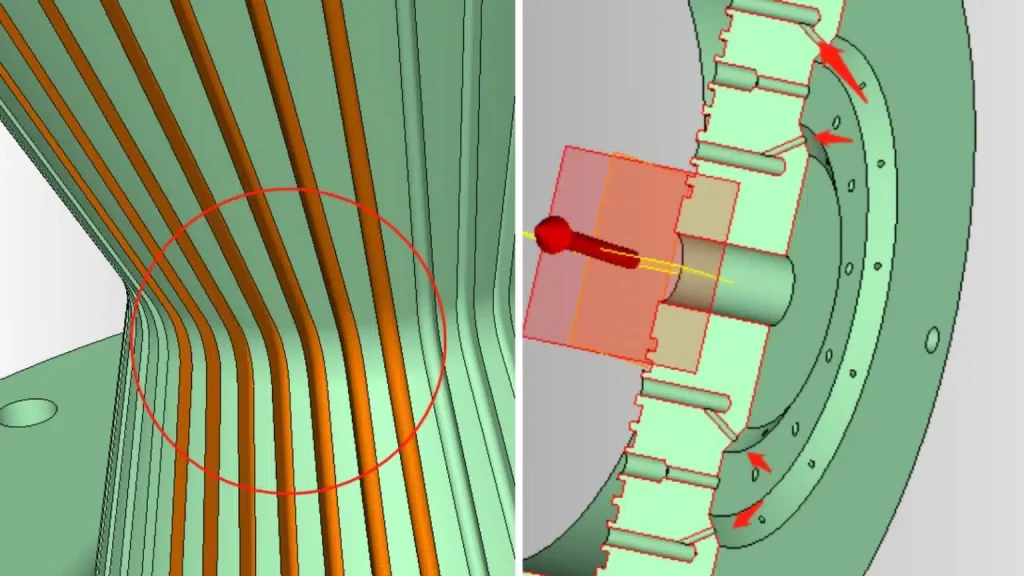
Fast-Tracking the Manufacturing Process
Time was of the essence. LURA had a tight schedule, aiming to participate in the Race to Space National Propulsion Competition. RapidDirect took this to heart. By leveraging their vast manufacturing network and prioritizing the Silverback Project, we reduced the production timeline drastically. From an initial estimate of 12 working days, RapidDirect streamlined the process, delivering precision-engineered components in a mere 7 working days.
Outstanding Results
LURA’s collaboration with RapidDirect bore fruit in the form of perfectly produced parts that were crucial to their success in the Race to Space National Propulsion Competition. The precision, quality, and craftsmanship of RapidDirect’s work not only met but exceeded LURA’s expectations, cementing its position as a trusted ally in the aerospace domain.
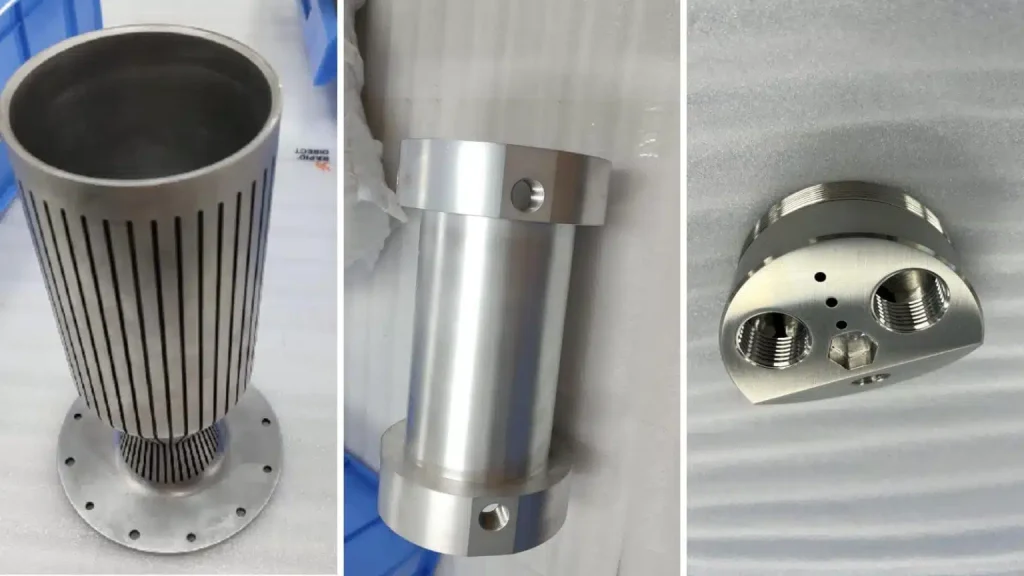
The collaboration between RapidDirect and LURA stands as a beacon of how the right partnership can elevate visions into tangible, award-winning successes. In the challenging arena of rocketry, it’s not just about having the right designs or ideas; it’s about finding the right allies to bring them to life. RapidDirect and LURA have indeed set a gold standard in this respect.
Future…
The LURA engineering team is on the brink of finalizing the design of Gryphon II, an imminent flagship rocket. Destined to shatter the UK’s amateur rocketry altitude record, it firmly positions LURA as a prominent leader among student rocketry teams nationally. RapidDirect cherishes the profound alignment with LURA’s innovative spirit and engineering prowess. Our journey, beautifully interwoven with shared ambitions and groundbreaking success, transcends beyond mere manufacturing alliances into a collaborative tapestry of exploration and innovation. With LURA on the brink of new astronomical feats, RapidDirect is thrilled to envision a future peppered with more complex, exhilarating projects, fostering advancements in rocketry technology and perpetuating an era of shared triumphs and discoveries.